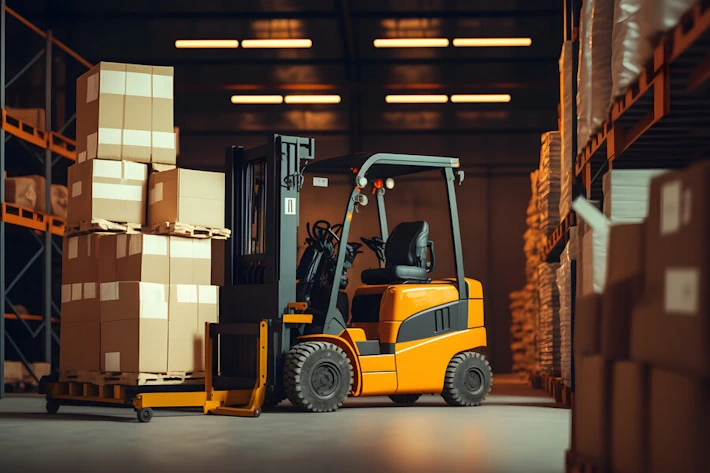
5 Ways to Improve Warehouse Forklift Safety
Forklifts are an important factor in maintaining warehouse productivity, but only when you observe the right safety precautions. Preventing forklift accidents should be a focus in your warehouse. With the right skills and mindset, you can improve warehouse forklift safety.