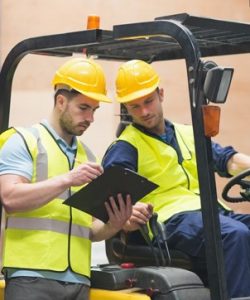
Forklift Safety Tips
Today’s blog covers several forklift safety tips you can use to help keep your operators, pedestrians, and workers safe. As important and useful as forklifts are to your business, they are equally as dangerous. OSHA estimates over 120,000 forklift-related accidents occur...