Any company that uses forklifts for material handling knows just how fast problems can snowball. Whether you have one truck, ten trucks, or one hundred trucks in your fleet the tools and approach to minimizing downtime are all the same. Today we are talking about how you can minimize your forklift downtime by following these simple tips.
DATA RECORDING
Simply put, the best way to achieve less forklift downtime is through effective data recording. Each company should be taking records of each forklift, as each forklift is different and will have its own unique problems. It is our recommendation to keep a separate record of each forklift. These records should show purchase or lease date, date obtained, brand, model number, serial number, all PM checkups, any part orders, and all repairs done by the service technician. Finally, you should keep track of engine hours, so you know how often the forklift is being used. These records will allow us to take a comprehensive look at your fleet and make informed decisions.
LIFE EXPECTANCY / COST PER HOUR
On average, the life expectancy of a forklift is about 10,000 hours. If you are running eight-hour shifts that averages out to around 2,000 hours per year or five years. Properly maintaining your forklift can ensure maximum uptime as well as extending its life beyond normal expectancy.
There are currently more than one million forklifts in use across America. It is estimated almost half of all forklifts in operation are operating at a higher cost per hour than needed and costing companies millions of dollars in unnecessary repairs. To know if you have a faulty forklift you must know two things, the ownership and maintenance cost of that forklift. Ownership cost is the difference between delivered cost and its residual value when turned in. For example, a truck that originally cost $15,000, is four years old and has accumulated 8,500 hours. Its trade-in value is now roughly $6,000. Subtract the trade-in value from the original cost it is now worth $9,000, the ownership cost, then divide by the engine hours. You will learn that this forklift costs $1.06 per operating hour.
The cumulative maintenance cost is a lot easier to calculate. Cumulative maintenance cost is the total of maintenance labor and material cost from the date of purchase. Let’s give another example, say your maintenance costs are $11,250. Again, divide this by the engine hours(8,500) to get $1.32, the maintenance cost per hour.
Add both costs together and you get your cost per hour to operate and maintain, in our example, the total would be $2.38 per hour.
KNOW WHEN TO REPLACE YOUR FORKLIFT
We have seen many businesses make the mistake of keeping a forklift that has outlived its usefulness. Or on the other spectrum, without information at their disposal, we see companies replacing forklifts at a certain age regardless of condition. The problem with this is that these companies are not taking a data-driven approach.
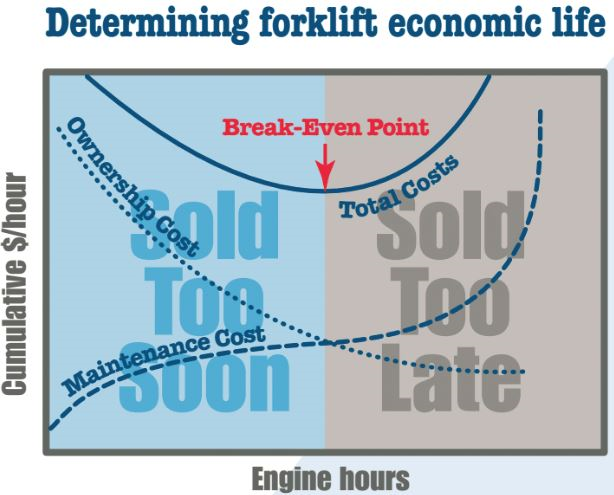
This chart is a good reference point on when to replace, as we can see the most cost-effective time to replace your forklift is when ownership cost meets maintenance cost. Past this point, the maintenance cost will rise and you may spend more than necessary to keep that forklift operating. Keep in mind this graph DOES NOT include the productivity lost and cost of downtime when the forklift is being repaired.
ENSURE YOUR FORKLIFT IS RIGHT FOR THE APPLICATION
Your business and material handling processes may change over time, but do your forklifts? Another common pain point we see is that the forklift specifications do not match the jobs they are expected to do. Perhaps you’ve outgrown your warehouse area and have started to store material on the floor or on the racks that may be farther than in the past.
For maximum effectiveness, your forklifts need to match the job required. If they don’t you could be spending more than necessary on keeping an overtaxed forklift running or spending extra on a forklift that is too powerful. You may also have too many forklifts and need to make cuts.
It is recommended to perform a thorough audit every three years, call and request one from us today! We can audit your operations at no cost.
EFFECTIVE PM PLANNING
It’s easy to relate forklifts back to cars because they have similar problems. You know that you wouldn’t drive your car for years without changing the oil or filters, so would you also do that to a forklift? You want to keep your car running well, so you maintain a proper maintenance schedule.
The same holds true with forklifts, if you follow a planned maintenance routine, you can reduce downtime and overall operating costs by catching problems before they happen. Small problems snowball, one day it’s a minor repair the next it’s causing significant downtime and problems for your operation.
Interested in learning more about PM’s? Contact our PM department today to get scheduled!
STAY INFORMED
With each forklift purchase comes an operation and maintenance manual, and within that you will find a maintenance section with scheduled service intervals. It will also provide service details on proper replacement fluids and service speculations. To ensure your forklift stays properly maintained for as long as possible, follow the manual.
Missing your manual? Contact us today to provide a new one!
IN CONCLUSION
Taking the proper steps to reduce forklift downtime can look overwhelming, but the money and time saved from reducing downtime are worthwhile. If you are interested in learning more or would like to speak with a Territory Manager in your area, then contact us today!